Solid Rocket Propellant Handling Facility
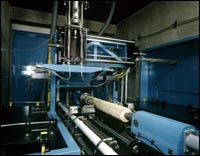
Extruded rocket propellant billets feed automatically into the Billet Turning Machine room through pneumatically operated explosion proof doors. Insertion of the billet into the Billet Turning Machine takes place via a pick and place. Turning of the outside diameter produces an on size billet that then exits into the next room.
PROJECT SCOPE:
Develop a facility to process extruded solid rocket propellant billets into finished grains suitable for use in rocket assisted projectiles, reducing labor from 140 people to 3 people while maintaining the same level of production and greatly increasing operator safety.
COMPANY:
A government ammunition facility operated by an internationally known ammunition manufacturer.
DESCRIPTION:
This facility consisted of seven different production processes, all controlled by one operator monitoring the system via computer. Two other operators loaded and unloaded raw and finished propellant. All machinery was located in explosion proof rooms, minimizing the operator’s exposure to any hazards.
UNIQUE FEATURES:
The system needed to be not only explosion proof but non-sparking and non-static generating. All machining functions included water flooding the process at a rate of 1000 gallons per minute. The budget for this project was minimal which necessitated a cooperative effort between the customer and Automation Plus in order to give the customer the most system for the money.
PROJECT DURATION:
This project lasted two years from initial concept to installation.
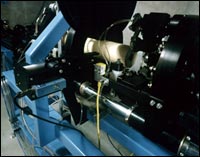
Turned to size rocket propellant billets feed automatically into the Spiral Wrapping Machine room through pneumatically operated explosion proof doors. Three layers of inhibitor plastic are solvent bonded to the outside diameter of the billet continuously.
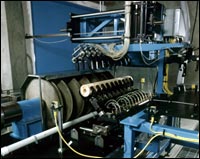
Plastic wrapped and cured rocket propellant billets feed automatically into the Grain Sawing Machine room through pneumatically operated explosion proof doors. Sawing of the billet by the Grain Sawing Machine produces multiple cake size units, or grains. A pneumatically operated pick and place releases these grains one at a time to the Grain Chucking Machine.
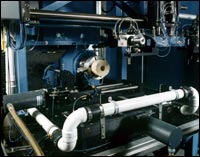
The grain travels from the Grain Sawing Machine via conveyor and a pneumatically operated pick and place loads them into the Grain Chucking Machine. The Grain Chucking Machine machines the face and bore to size. The grain travels from the Grain Chucking Machine via conveyor and into the End Inhibiting room through pneumatically operated explosion proof doors.
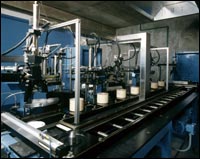
The End Inhibiting Machine automatically solvent bonds a plastic inhibitor disk to both ends, cupping the disks during application on the grain to prevent air entrapment. The grains at this stage have plastic completely encasing them.
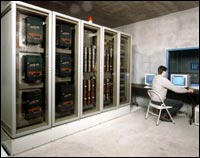
One operator monitoring the system via computer controls all seven operations. Multiple-level password system and in-process monitoring protects the entire system from errors.